When we purchased our Airstream we got a good deal by buying one ordered by another customer who backed out of the deal. Lucky for us, they had opted to have every awning possible. We’ve got two manual awnings on one side, one in the back, and a big powered Zip Dee Relax on our entry side. Up until now, they have all served us faithfully, providing much-valued shade on sunny days.
It all began innocently enough
But in July of 2017, our Relax 12v Automatic Zip Dee Awning no longer zipped. While closing the power awning it suddenly stopped in its tracks and refused to budge. A quick inspection showed no obvious problem so we pulled our trusty owners manual to see what we could sort out. One of the joys of an American-made product is a cogent owners manual. Alas, despite its clarity and helpful diagrams, it offered no sure diagnosis for the problem we faced.
Our next step was to call Zip Dee customer service. We were able to get ahold of a technician right away, another delightful novelty in the world of consumer products. We explained the symptoms as we saw them and answered a couple questions from our tech to get at the root of the problem Zip Dee service declared that the roller motor was likely dead and the cause was an outdated motor controller board. If you own a newer Airstream as we do, you will find it under the sink. We were happy to learn that a new board and a repaired motor would be covered under warranty.
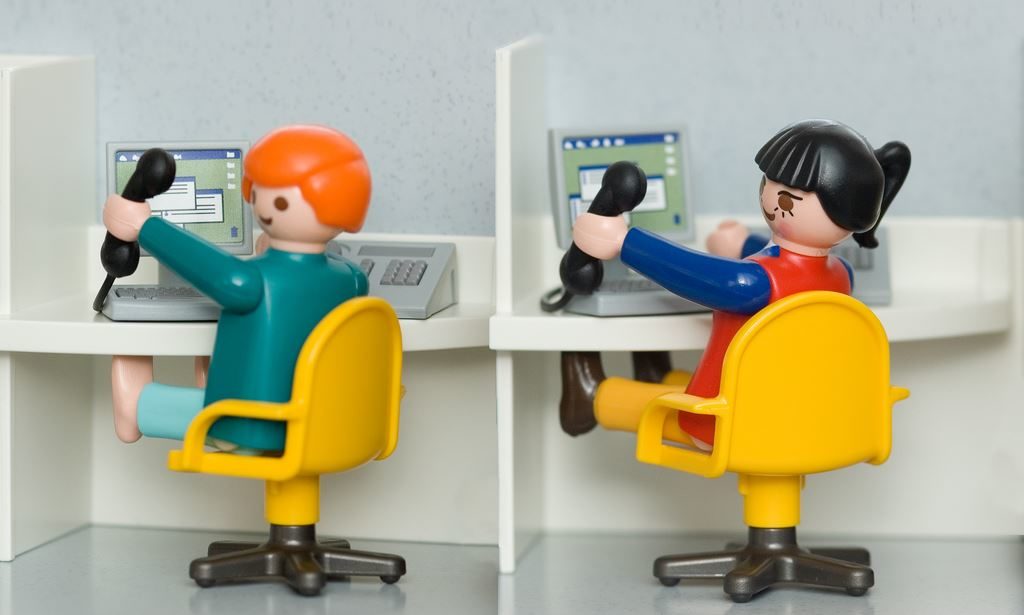
Trouble with your awning sir? Have you tried turning off and back on again? Are you currently taking any pain medications? I think this might be a metaphysical problem sir, I’ll have to call in a supervisor.
And then the trouble started
Until we could get our awning repaired, we would need to get it ready for travel. Having an open sail attached to your Airstream is not a great way to travel down the nation’s highways. With the motor broken, it didn’t want to budge. No worries, our helpful Zip Dee serviceman was there to help by phone. “First thing,” he says, “you will need your emergency repair kit.” He described it to us: a crank device, a funny screw type thing, and a set of cables with alligator clips. Trail had been through every inch of our trailer and we had no such kit. A little fruitless searching later and we confirmed that our dealer had neglected to include it.
“We can still do this,” our serviceman optimistically stated, “All you need is a 20 thread 1/4th-inch bolt at least 2 inches long.” We didn’t have one of those but there was a Home Depot not too far away. He went on and explained the general procedure:
- Remove the two air-piston braces.
- Put the 1/4-20 x 2″ bolt into a hole in the end of the roller to serve as an axle.
- Find and remove the black, hardened steel safety bolt (aka a 10-32×1 1/2″ hardened carbon steel phillips head machine screw with nylock hex nut) near where the roller connects to the arm. Be sure to hold onto the awning as it will want to roll up. Slowly allow it to roll up and retract.
- Finally, put the hardened steel bolt back in place.
Easier said than done
We went to the Home Depot and got a couple bolts of different lengths and returned to our trailer. We found our owners manual also had instructions for manually retracting the awning. In addition to what we were told, it informed us we needed to unplug the cord connected to the roller. Reading is good. We got our new bolt put into the end of the roller and started in on the removing the hardened steel retaining bolt.
The black bolt of doom – as it was soon to be named – had a Phillips screw head on one end and a nut and washer on the other. The nut and washer came off easily but it would not turn with a screwdriver. I tried harder, still no luck. I got out the torque driver, no good, and by now the bolt head was getting pretty stripped out. Meanwhile, Trail was trying to remove the bolt on the other end. I was pretty sure we didn’t want to do that. I decided another call to Zip Dee was in order. They confirmed only the bolt near the motor should come out, and that if it was stripped, then we might have to push it out.
The only thing I could find that would work to drive it through was a thin screwdriver and a hammer. Figuring I could make quick work of it I got started. After about 5 minutes hammering away, the screw moved about 1/8th of an inch, the handle on the screwdriver was hot to the touch. I expected it would shatter at any moment. We went back to the Home Depot again. This time we found a couple of hardened steel punches to drive out the bolt.
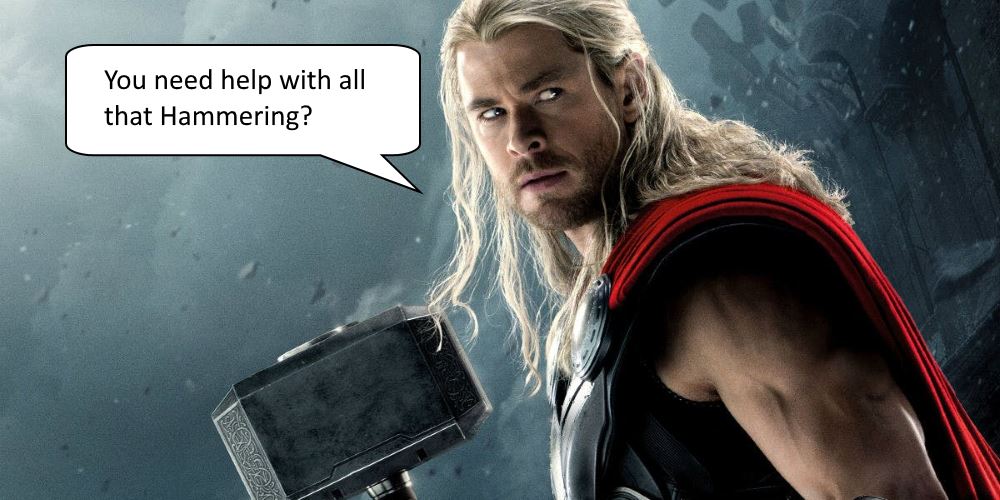
No thanks buddy, I think I got it! Go save the universe or something before my wife sees you!
If brute force isn’t working, you’re not using enough
On returning I got back to my hammering. I really put a whack on the punch and finally budged the black bolt of woe, driving it half way out of its purchase after many whacks. But then it stuck fast. I hammered on it until visible smoke started to come out of the hole and the punch bent at a 15-degree angle. Mystified, and frustrated, I called Zip Dee again. They were surprised it would not come out but assured me it was the only way forward. Whatever it took, I needed to get the thing out!
I tried pulling on it mightily with a pair of pliers. I bent the hardened steel bolt of misery but it didn’t come out of its hole. What unholy force held it in place? It was time to stop and ponder carefully. I used a flashlight to peer into the depths. I removed the axle bolt and tried probing the hole with the non-bent steel punch. I fiddled around with the roller to see if there was any way to roll it up manually. It took great force to turn the spring loaded roller. Finally, it hit me. I realized the bolt was threaded through an exterior tube and an inner tube on the roller. The bolt of suffering’s job was to keep them aligned. Once pulled, it would free the inner cylinder to spin and thus roll up.
The obstruction I could see in the hole was the inner metal tube, half turned, which meant on the side still stuck, the tube was pinching the steel bolt in place. freeing the bolt half way had really put the bite on the other side as all the springs force was now on that one point. I had trail come grab the bolt of endless sorrow with the pliers while I used my hands to twist the roller, aligning the inner and outer tubes. The blackest bolt of lamentation and pain finally came free, bent, stripped, and gouged. Sure enough, free of the bolt the roller strained to spin up, so we carefully allowed it to roll up and the awning was closed at last.
Revenge of the bolt
But now we had this busted bolt, and both the manual and the Zip Dee tech had insisted it was essential to put it back in for travel. For the third time, we drove to Home Depot, this time to get a replacement bolt. They don’t have hardened steel bolts it turns out, Zinc was the best we could do. We also needed a ladder. We’d talked about getting one for a while, but never actually needed it. There was no way we were getting that bolt in the retracted awning without one. Pondering the selection, we ended up with a cool folding extension ladder for around $120 that could actually support my 300lb enormity aloft.
We set up the ladder and climbed up to put the bolt back in. Knowing my enemy, I looked to see if the inner and outer shafts were aligned. They were not. The only way I had to align them was to pull the awning out a few inches, then the bolt went in just fine… but the spring on the roller was what was holding it fast to the Airstream so now it hung out with the bolt in place. With a sigh, I removed the replacement bolt, that’s when the arm came detached from the roller. Grabbing it quickly, it became clear that this was why we really needed to have this bolt in there, it not only kept the roller set, it also held the arm on.
Strapping one on
We called Zip Dee again and explained our situation. The now, very familiar service technician let us know that no other bolt should ever be used that is not hardened steel (and thus evil incarnate). Any lesser bolt would be sheared in half by the spring before long. He explained that what we needed to do, was to get some rope and bind the two arms of the awning together so that they could not come off the roller in travel. Then we should be good to go. We pulled out our handy dandy cargo straps and… they were not long enough to loop both ways on the 28′ long awning. Yay, back to Home Depot for trip #4!
Weary and frustrated we pondered various ropes and straps. Trail picked out two 28′ cargo straps while I grabbed a backup, a 100′ of nylon rope. We got back and started working on the straps. Again we ran into issues. While the straps were long enough, they came with open S hooks on the end which had two problems. Firstly they would not be totally secure for straps going side to side rather than up and down, secondly, they would hang loose and slap into the delicate surface of the airstream. Anne noticed me playing with the carabiner that came with my rope and realized that would be the ideal fastener, only we needed two more of them. So… Trip #5 to Home Depot, this time for carabiners, tape, zip ties, and polishing cloths.
Trail used the polishing cloth to wrap up the connecting pieces and carabiners on the straps so they wouldn’t damage the airstream. The Zip ties held those securely in place. She’s pretty brilliant at such things and it worked like a charm. We also ran a line over the top of the trailer to tie our broken awning to one of the manual ones on the opposite side just to ensure the power awning couldn’t open up in the wind. At long last, we were good to travel with our broken awning. Now, all we had to do was reorganize everything in our truck bed to try and make room for the new ladder and the two 20 air piston arms we had to remove from the awning to get it closed.
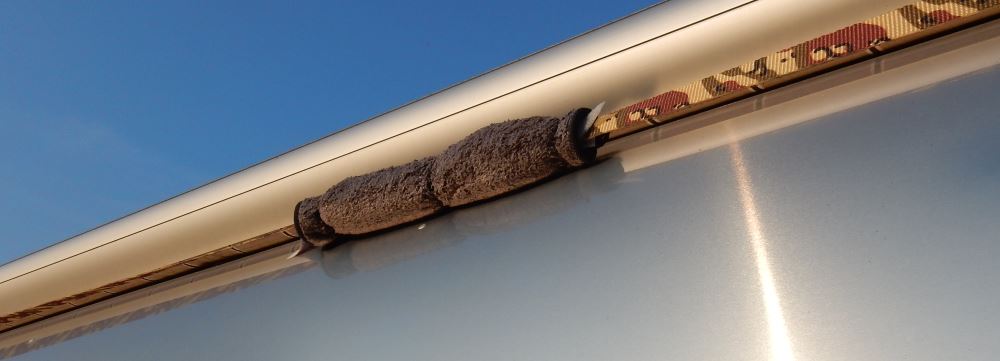
Inside the soft and secure wrapper are hooks, buckles, and other scratch and dent happy contrivances.
And it’s not even fixed yet
Next up was to make an appointment to get the thing fixed. The challenge with service appointments is you typically have to make them well in advance. The challenge with that is we don’t always know where we will be well in advance. I had already made some appointments to see a friend a week later, so staying put wasn’t an option. Trail put her navigation super powers to work and came up with a list of possible service stops along the east coast, along with the date by which we could get to them. My job was to start calling until we could get an appointment that would line up with the time frame under which we could arrive, but not so late that it would cause a significant delay.
After a few calls, I finally found a service center that would do Zip Dee warranty work, that could get us an appointment in the right time frame, and who didn’t sound like they were annoyed by the act of having to schedule a service appointment. I’d think that last bit would be rare, but it wasn’t. A lot of them only begrudgingly would agree to even look at it, much less commit to fixing the problem. Fortunately, the friendly folks at Restless Wheels RV seemed to be eager for the business and after calling Zip Dee to confirm the could be reimbursed, made an appointment for us.
The final chapter
Three weeks later we make it safe and sound to Restless Wheels RV. Trail’s brilliant strapping work has done its job flawlessly. The battle of the bolt is little more than a fevered memory. Trail is having premonitions of ordering parts, waiting for weeks, and otherwise having Murphy’s law nightmares. Arriving at Restless Wheels RV, the vast number of deep gouges in the roadway coming in and out of their driveway seem like an ominous omen. How many trailers have come here to die?
We left our home in their care after explaining the particulars of the problem. Seeing a Dodge dealership right next door, we decided to take the Truck in for a brake inspection while we awaited our fate. After getting a call while waiting for the truck, I walked over to find out what happened. Apparently, the heavens had decided to send good luck our way.
It turns out that Restless Wheels had just recently replaced another awning like ours, which left them with a brand new control board, one of the components the manufacturer felt we needed to replace. The new control board fixed all our problems. The motor wasn’t broken after all, and they found a new bolt to replace that dreaded implement never to be spoken of again. We were good to go and Zip Dee covered the entire cost so we owed not a cent!
New brakes on the truck, however, would cost us a cool $450. You win some, you lose some. All said, big props to Restless Wheels RV for fast friendly service and to Zip Dee for standing by their product and doing right by their customers. Both companies made this horror story a lot less horrifying for us.
3 Comments
THANK YOU! Saved us today when we had a similar problem. Found the stupid head bolt and we were able to get it out without destroying anything. Head bolt is back in with arms in and now we move down the road.
I’m so glad we could be helpful, save travels!
Glad it all got resolved. If it ever happens again…to find hardened bolts in a small town area…don’t go to Home Depot, its for household repairs, instead go to an auto parts store. Hardened bolts do get used in auto repair situations but not typically for home repair. Sometimes they can be found in the small hardware screw/bolt/ oddity items bins/drawers at hardware stores such as Ace, True Value or Do-It-Best chains. Generally speaking go to a regular hardware store such as those just listed for your hardware items. In the auto parts stores things such as special bolts are likely in the stock area behind the counter rather than out on the racks, just because you don’t see them does not mean they don’t have them 🙂